Reduce Antimony Oxide Loading by Up to 50% Without Compromising Flame Retardant Properties
Reading Time: 3 minutes
For years, manufacturers in a range of industries have been using antimony oxide and antimony trioxide (ATO) to enhance the effectiveness of a halogenated flame retardant. As the United States no longer mines antimony since the closure of the Sunshine Mine in Idaho in 2001, it relies heavily on China imports.
In September, China implemented stricter export restrictions on six antimony-related products including antimony ore, antimony metals, antimony oxide and gold-antimony smelting and separation technologies. Now, exporters must apply for a license through China’s Commerce Ministry.
Supply disruptions from China along with recent price increases require companies to find alternatives to antimony oxide as a flame retardant enhancer. One such alternative is Sidistar® polymer additives from Elkem Materials. Keep reading to learn about the benefits of using Sidistar products for your formulation.
Reduce Production Costs
Sidistar can significantly lower production costs while maintaining or even improving performance. You can replace up to 50% of ATO with Sidistar additives without compromising flame retardant properties or physical characteristics.
Sidistar offers substantial savings due to its lower purchase price. Another benefit of Sidistar is that it is ~60% lighter than ATO (density 2.2 vs 5.2). This reduces the weight of the finished part, resulting in further cost savings.
For example, if you need 100,000 lbs of ATO at a cost $12.00 per lb, the total cost would be $1,200,000. By replacing 50% of the ATO with Sidistar, you can save 25% of your total spend.
We have a cost calculator to calculate the potential savings for your specific formula, so contact us for an estimate.
Inhibit the Spread of Flames
To understand how Sidistar can improve your flame retardant performance, let’s explore how halogenated flame retardants typically work to prevent the spread of flames. This process involves three key phases:
Gas Phase Reaction
The flame retardant disrupts the combustion process in the gas phase by cooling the system, which reduces and limits the supply of flammable gases.
Mesophase Reaction
This occurs at the interface between the gas phase and the condensed phase during combustion.
Condensed Phase Reaction
In the solid phase, the flame retardant forms a protective char layer, smothering the material and cutting off the oxygen supply. This char acts as a barrier against heat sources or flames. Sidistar products are often used to boost char formation in this phase.
The graphic below illustrates the reactions occurring during all three phases.
Improved Dispersion and Char Formation
Unlike other nano-sized materials, Sidistar is easily dispersed using standard equipment, such as twin-screw extruders or kneaders, breaking down to primary particles. This unique property ensures excellent dispersion in the polymer matrix.
Sidistar also enhances char formation, making it stronger and more compact. When combined with other flame retardant additives, Sidistar improves their efficiency, strengthens the char, and reduces smoke production and the formation of burning droplets in tests like the UL 94 vertical burn test.
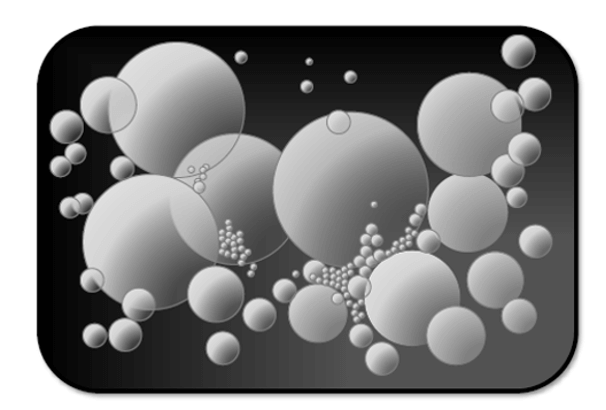
This improvement in char formation can be explained by the particle packing theory. smaller particles fill the gaps between larger ones, increasing packing density and resulting in a stronger char layer.
H.M. Royal offers high-quality Sidistar products to meet your flame retardant needs. Are you interested in seeing how much you could save by replacing up to 50% of antimony oxide with Sidistar? Contact an H.M. Royal expert today to learn more.